Concerning Industrial Fans, you cannot help dealing with ATEX, sooner or later.
This acronym (made up by the first letters of the words ATmosphéres and EXplosibles) identifies two different directives of the European Community:
- No. 2014/34/UE, that became law on the 30th March 2014, which regulates the devices and machinery working in potentially explosive atmospheres, and is directed to manufactures of devices destined to be used around potentially explosive atmospheres; the manufactures must certify these products: the directive before, Directive No. 94/9/CE, has been canceled by this new one, starting from the 20th April 2016;
- la 99/92/CE, which is directed to the users of certified devices and concerns safety and health of the workers in potentially explosive atmospheres: it is implemented in backgrounds where explosions can actually occur.
The ATEX Regulations indicate the essential requirements that the devices must have concerning safety and health: you can easily realize that respecting these requirements is essential for industrial fans that are installed in backgrounds where explosions can potentially occur.
The main suppliers of industrial ventilation systems, including Euroventilatori International, supply certified ATEX fans equipped with all necessary technical documentation.
Before installing an industrial fan you must evaluate the risks concerning the background where the fan is going to work. However, the choice of installing an industrial fan that meets the requirements of the ATEX directive is completely up to the Customer.
In this case, a supplier like Euroventilatori International can best assist and advise the Customer, thanks to its staff of highly qualified technical experts.
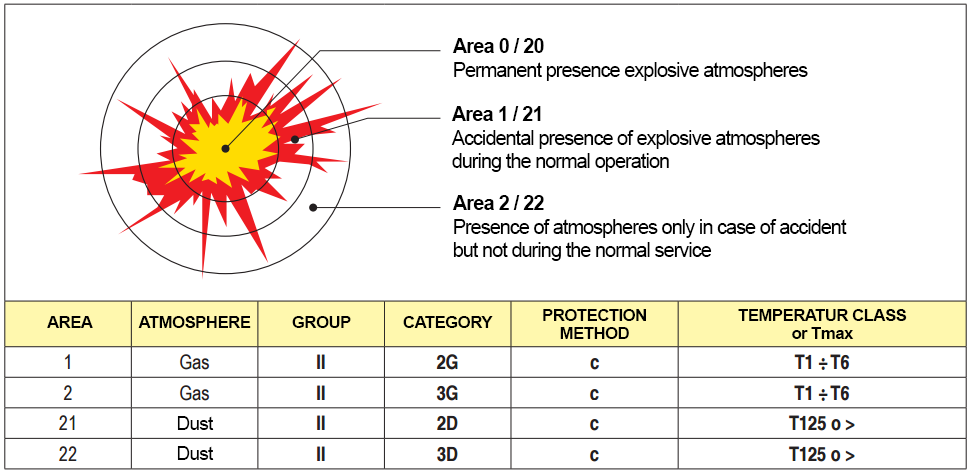
The ATEX zones chart
The fans that meet the requirements of the ATEX directive are built following some particular expedients in order to avoid sparks caused by the friction between the spinning part and the fix one; there are different parts and characteristics that are accurately examined before assembling the fan.
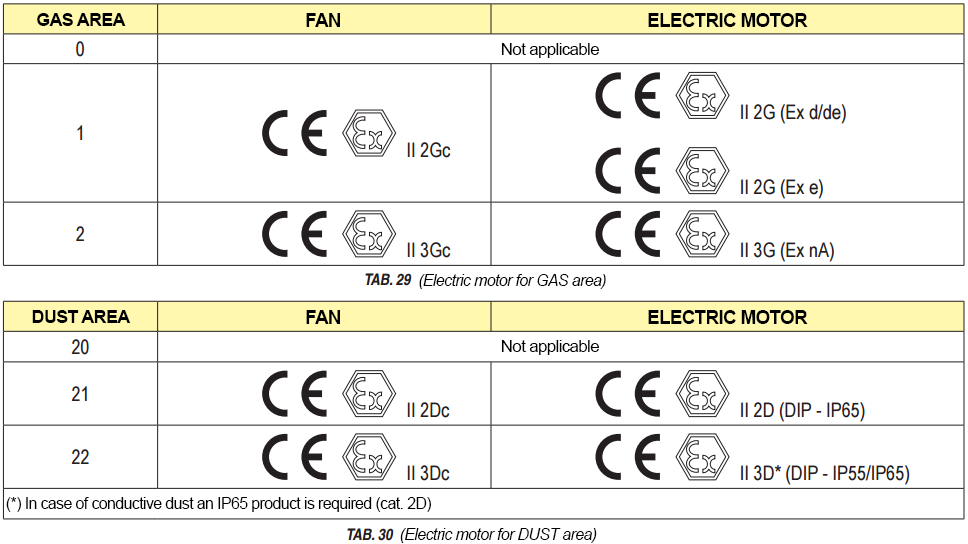
Depending on the background , the ATEX directive indicates the Fan and Motor Type
Furthermore, once the devices are working, accurately planning the maintenance and the cleaning is of fundamental importance, depending on the type of background where the fan works and depending on the materials that are eventually driven in it: dusts are potentially dangerous, because they set down even where mobile and fixed parts are closer and can therefore cause sparks.
Euroventilatori International provides, together with its own certified ATEX fans, all certifications and technical manuals which are necessary in order to best use the device; it can also assist its Customers in extremely short times, through the intervention of its highly qualified staff.