When you talk about the discharge position of an industrial fan you actually refer to the position of the discharge, or rather the output air flow.
An industrial fan is just one of the various elements that make up the ventilation system where it is integrated: in order to convey the air flow, the fan will obviously have to provide a ductwork, and especially both income and output pipes.
The incoming air flow (suction) is almost always clearly defined, while the output air flow (discharge) can be oriented in many different directions, up or down, right or left or even in intermediate directions.
Keeping the other elements unchanged, the shorter the ductwork is, the more effective it is: as a consequence, the choice of the discharge position is generally up to the plant engineer, which can accurately evaluate all the involved features and properly take into consideration the interactions between the various elements of the ventilation system.
The possible discharge positions are determined, according to international regulation, with an alphanumeric code where the literal part (RD or LG) indicates the direction of rotation of the impeller and the number indicates the angle of the output air flow.
The typical discharge positions are 16, where 8 of them are clockwise rotation (RD) and the other 8 ones counterclockwise rotation (LG): keep in mind that in a centrifugal fan the discharge position must be determined by looking at the fan from the motor side.
Euroventilatori International produces industrial fans in 16 different positions of the delivery mouth: some discharge positions, and precisely RD – LG 180 and 225 are constructed implementing special building adaptations.
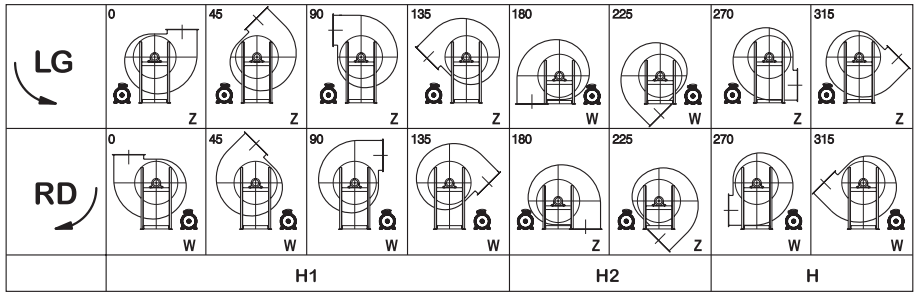
Discharge position of industrial fans in indirect transmission
Concerning not direct driven fans (all fans with constructive executions where a belt or some other components for transmission are involved to bond the impeller and the motor), the related discharge positions can be chosen according to the standard angles that you can see on the picture.
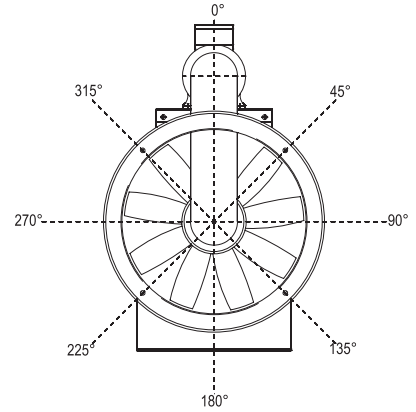
Discharge position of axial industrial fans
In axial fans the angular position of the motor is indicated by the angle (in degrees) between the reference axis orthogonal to the supporting base and the accessory element axis, rotating on the axis of the fan from the point of view of the control side.
The choice of the right discharge position is essential in order to get the best performance from the ventilation system: the right directioning of the discharge will effect the output pipes, which can therefore be as short as possible. That’s why choosing experienced and capable builders of industrial fans, like Euroventilatori International, is fundamental: we can actually provide assistance to our customer since the very first selection phase of the fan which better suits his needs, and assist him all the process of planning and accomplishing of the ventilation system long thanks to our own technical department, our plant engineers and technical experts.
Choosing an industrial fan producer that can assist the customer step by step during the accomplishment of the ventilation system means implementing a really custom-made ventilation system, which has actually been designed on the customer’s needs, that will therefore guarantee the best return of investment and achieved results.